浅谈传统印前打样常见的问题及解决方法,作为条码印刷厂家,关于不干胶标签的特点和应用也是有一点理解的。我们先要了解一下什么是不干胶标签的印刷,它与传统标签印刷相比有什么不同。不干胶标签也叫自粘标签,及时贴,即时贴,压敏纸等,是以纸张,薄膜或特种材料为面料,背面涂有粘合剂,以涂硅保护纸为底纸的一种复合材料,并经印刷,模切等加工后成为成品标签现在手机市场已经非常火热了,而且众多的手机品牌和种类都开始出现,满足了人们的购买需求,与此同时,手机包装盒也是非常重要的,那么手机膜包装盒印刷方式有哪些?下面远鸿印刷说一下。手机膜包装盒印刷 钢化膜包装盒定制时需要注意什么细节 1,钢化膜包装盒设计主题要明确,分清主次,突出产品特性,当一个产品钢喝药酒的好处不少,这使得一些爱好养身的人都有饮食药酒的习惯。为了确保药酒的质量,也为了提升药酒的销量,企业需在药酒包装盒上功夫。那么药酒包装盒定做哪家好以及喝药酒的好处又有哪些呢? 药酒包装盒定做厂家推荐 药酒包装盒定做厂家小编推荐远鸿印刷公司,因为远鸿印刷公司是一家专业生产以及销售各类包装盒的
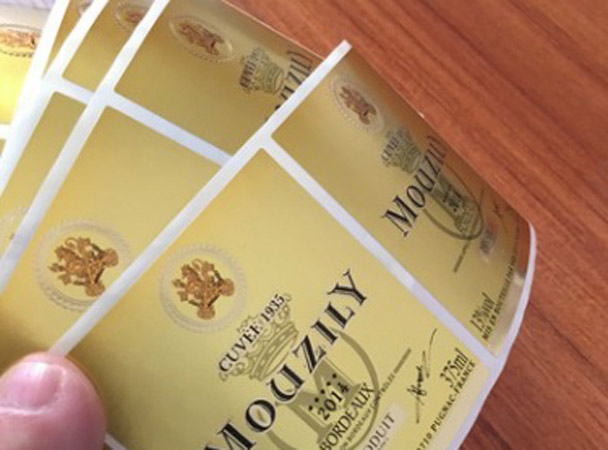
浅谈传统印前打样常见的问题及解决方法,打样是模拟印刷、检查印版阶调与色调能否取得良好的合成再现,并将复制再现的误差及应达到的数据标准,提供给印版,作为修正或再版时的依据,同时,为彩盒印刷的墨色、墨层密度及网点增大数据提供参考样张,并作为编辑校对的签样样张。
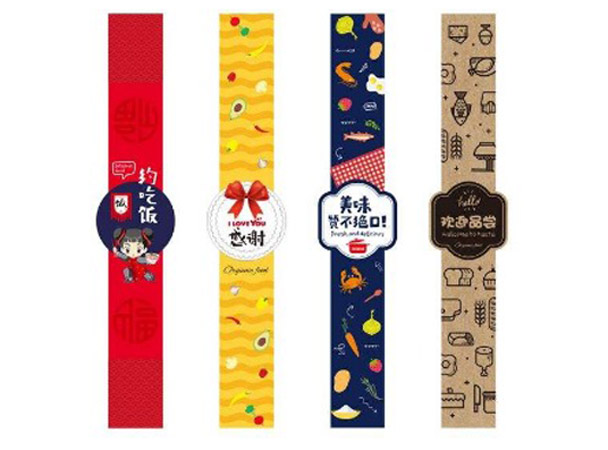
此外,打样更是制版和印刷之间连接的桥梁,它的质量好坏,直接影响制版和印刷品的质量。 就目前来说,彩色打样的方式有很多,不过国内各印刷厂主要使用的仍是传统机器打样。然而,在传统机器打样中经常会遇到一些问题,以至于印刷效率降低,有时候还会影响产品的质量,为了让更多朋友尽可能的避免这些问题的出现,下面远鸿为大家总结了以下一些关于传统印前打样常见的问题及解决方法,供大家参考! 一、网点增大过多 尤其是夏天,室内温度过高,若没有空调设备,必然造成油墨流动性加大,一般解决办法是在墨内加入2%的号外油,使油墨的黏度增大;然后将版台制冷的温度适当降低1~2℃,增加油墨的凝结力,这样处理后,网点的增大率会得到很大的改善。另外造成网点增大的原因还有以下几点,大家应注意掌握。 (1)版台压力过大 版台压力建议在0.1~0.11mm范围内,而纸台压力应在0.12~0.13mm范围内,这对改善网点增大过多有好处。 (2)水分过大 水分过大,墨就印不上,要印上墨,墨就要配稀,墨量就要加大,必然造成网点增大过多。因此,操作时必须控制水分。 (3)墨量太大 有时由于版浅,为了追原稿,不按规范数据操作,过多地加大墨量,造成网点增大过多。因此,任何情况下都要严格按规范数据操作,不能借深、借浅,原版太浅应改进原版。 (4)墨辊压力过大,墨辊老化,墨辊本身抓不住墨。应及时按标准调整墨辊压力,墨辊与版台压力调至6mm,墨辊与串墨辊压力调至4mm。并及时更换墨辊。 (5)橡皮布老化 橡皮布用的时间过长,表面氧化,弹性减弱,表面光滑。用这样的橡皮布打样,油墨吸附性差,传递性能不好,必然造成过多的网点增大。因此,出现橡皮布老化时应及时更换新的。 二、网点出现空心 有时打样网点增大过小,点心出现空心,这种情况的出现可以从以下几点原因着手解决。 (1)PS版粗糙,砂目太粗。 (2)压力不合适等。 (3)冬天由于室内温度低,相对湿度小,操作时,印版台的制冷调得过低,油墨黏度大,油墨在版上由于过冷而凝固,橡皮布在转移油墨时,将印版上的墨拉起,四周被拉起而中心缩回到印版上,就造成了网点中心有小白点。 解决办法是: (1)在油墨内加5%撤淡剂,使油墨滋润而流动度适当。 (2)要选用砂目均匀、粗细深浅适度的PS版材。 (3)可适当提高版台的温度。 以上几点便是在打样中经常会出现的一些问题,只要我们注意这些问题,那么在彩盒印刷中的效率就会提高,而且印刷出来的质量也会更好!远鸿专业从事彩盒、包装盒等方面的印刷服务,具备多年的丰富经验,技术精湛,报价公道,如有需要,我们随时为您效劳!
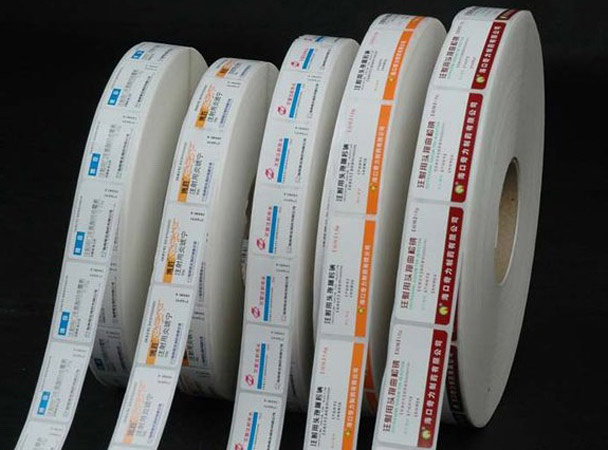
浅谈传统印前打样常见的问题及解决方法由咸宁不干胶印刷编辑https://www.jinnuo668.com/xianning/810.html 如需转载请注明出处
贵州印刷 中山印刷 达州印刷 黔东南州印刷 杭州印刷 神农架印刷 天门印刷 文昌印刷 唐山印刷 佛山印刷 湖州印刷 武汉印刷 新疆印刷 河南印刷 临夏印刷
助孕公司哪家靠谱 做助孕有危险吗 国内都有哪些助孕公司 助孕在线咨询 哈尔滨助孕 包成功助孕多少费用 哪里的助孕便宜 厦门助孕 专业助孕公司电话 国内助孕价钱 专业的助孕机构费用 正规助孕费用 国内助孕哪家比较可靠 助孕身体具备条件 大连助孕 杭州助孕 国内最好的助孕公司 哪里有助孕妈妈找 国内10大助孕机构 有好的助孕公司吗